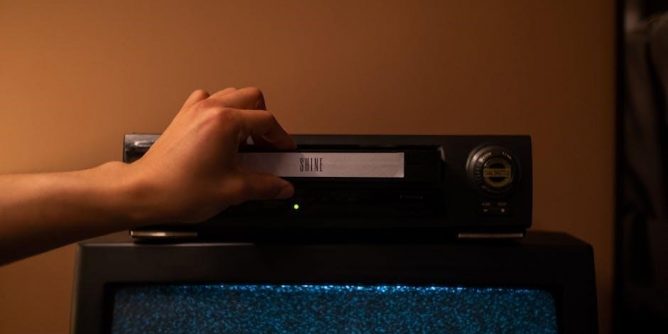
The Lycoming O-360 is a four-cylinder, air-cooled aircraft engine widely used in general aviation. Known for reliability, it powers aircraft like the Cessna 172 and Piper Cherokee. The overhaul manual provides critical guidance for maintenance, ensuring optimal performance and safety.
1.1 Historical Background and Development
The Lycoming O-360 engine was introduced in the 1950s, becoming a cornerstone of general aviation. Designed for reliability and versatility, it powered iconic aircraft like the Cessna 172 and Piper Cherokee. With a 180-horsepower output, it quickly gained popularity for its durability and performance. Its development included innovations like a direct-drive system and a robust air-cooling design. The O-360’s success led to variants such as the IO-360, featuring fuel injection. Its enduring relevance underscores its importance in aviation history and maintenance practices.
1.2 Key Features and Applications
The Lycoming O-360 is a four-cylinder, horizontally-opposed, air-cooled engine, producing 180 horsepower. Its compact design makes it ideal for small aircraft. Fuel-injected variants enhance performance. Widely used in trainers and personal aircraft, it’s known for durability. Regular overhauls ensure longevity and safety. Operators rely on its consistent power output. Its versatility suits various aviation needs. Critical components require precise maintenance. Adherence to manual guidelines is essential. The O-360’s reliability has made it a favorite in general aviation.
1.3 Importance of Regular Overhaul
Regular overhauls are crucial for maintaining the Lycoming O-360’s performance and safety. They prevent premature wear and potential failures. Overhauls involve inspecting and replacing critical components, ensuring compliance with aviation standards. A well-maintained engine reduces operational risks and extends service life. Proper overhaul procedures, as outlined in the manual, are essential for reliability. Regular maintenance also helps in detecting issues early, preventing costly repairs. Overhauls are vital for ensuring the engine operates within safe and efficient parameters. They are a key part of aircraft safety and performance.
Pre-Overhaul Preparation
Pre-overhaul preparation involves gathering tools, reviewing manuals, and ensuring a safe workspace. Specialized tools and proper documentation are essential for a successful overhaul process.
2.1 Tools and Equipment Required
The Lycoming O-360 overhaul requires specialized tools, such as a torque wrench, piston ring compressor, and micrometers. Essential equipment includes an engine stand, bearing puller, and valve spring compressor. Additional tools like a dial indicator, plunger lift gauge, and crankshaft locking tool are necessary for precise measurements and component removal. A parts washer and cleaning brushes are also needed for thorough engine cleaning. Proper tools ensure compliance with manual specifications and prevent costly errors during disassembly and inspection. Always verify tool calibration before use.
2.2 Safety Precautions and Workshop Setup
Ensure a clean, well-lit workspace with proper ventilation to prevent fume inhalation. Wear protective gear, including gloves and safety glasses. Secure the engine on a sturdy stand to avoid movement. Disconnect and label all fuel and electrical connections to prevent accidental start-up. Use jack stands and wheel chocks for aircraft stabilization if overhauling on-wing. Keep fire extinguishers nearby and avoid open flames. Follow all torque specifications to prevent component damage. Regularly inspect tools for wear and ensure they are in good working condition. Proper setup and safety practices minimize risks during the overhaul process. Always refer to the manual for specific guidelines.
2.3 Documentation and Manual References
Consult the Lycoming O-360 Overhaul Manual (Part Number 60294-7-9) for detailed procedures. Refer to the Operators Manual for engine specifications and maintenance guidelines. Ensure all Service Bulletins and Airworthiness Directives are reviewed and complied with. Maintain detailed records of inspections, repairs, and parts replaced. Use torque specifications and alignment guides provided in the manual; Proper documentation ensures compliance with aviation standards and enhances safety. Always cross-reference with the latest updates from Lycoming’s product support network.
Engine Disassembly and Inspection
Engine disassembly involves removing components like cylinders, crankshaft, and camshaft. Inspect for wear, cracks, or damage. Measure critical parts against overhaul limits.
3.1 Step-by-Step Disassembly Process
The disassembly begins with draining the oil and removing the accessories. Next, disconnect the fuel and ignition systems. Carefully remove the cylinder heads and pistons, followed by the crankcase and crankshaft. Each component is documented and inspected for wear or damage. Special tools are essential for procedures like valve train removal. Following the manual ensures all parts are correctly labeled and stored for reassembly. Attention to detail is crucial to avoid damage during the process.
3;2 Inspection of Critical Components
The inspection phase involves examining the crankshaft, camshaft, cylinders, and pistons for wear or damage. Measure the crankshaft for ovality and the camshaft for lobe wear. Check cylinders for scoring or excessive wear, and piston rings for proper sealing. The valve train is inspected for worn or bent components. All parts are compared against Lycoming’s specifications to determine if they can be reused or require replacement. This step ensures only airworthy components are retained for reassembly.
3.3 Measuring and Assessing Wear Limits
During overhaul, precise measurements are taken to assess wear on critical components. The crankshaft and camshaft are checked for ovality and lobe wear using micrometers and dial indicators. Cylinders are measured for taper and out-of-round conditions using a dial bore gauge. Piston rings and connecting rods are inspected for excessive wear. All measurements are compared against Lycoming’s specifications to determine if components are within acceptable limits or require replacement. This step ensures compliance with manufacturer standards for safety and performance.
Overhaul Procedures
The overhaul involves rebuilding critical components like the crankshaft and camshaft, replacing cylinders, and reassembling the valve train. Each step follows precise Lycoming specifications to ensure reliability.
4.1 Rebuilding the Crankshaft and Camshaft
Rebuilding the crankshaft involves inspecting for wear or damage, grinding if necessary, and re-nitriding. The camshaft is examined for lobe wear and replaced if beyond limits. New bearings and seals are installed during reassembly, ensuring precise torque specifications. This process restores the engine’s core components to factory standards, guaranteeing reliable operation and longevity; Proper alignment and lubrication are critical during reinstallation to prevent premature wear and ensure smooth engine performance.
4.2 Cylinder Replacement and Honing
Cylinder replacement begins with removing the old cylinders and inspecting for cracks or excessive wear. Stuck cylinders may require a hydraulic press for safe removal. Honing involves using a Sunnen-style hone to achieve the correct surface finish, ensuring proper piston ring seating and oil retention. The process is followed by a thorough cleaning to remove metal debris. Final inspection confirms the cylinders meet Lycoming’s specifications for ovality and taper before reassembly.
4.3 Reinstalling the Valve Train and Accessories
Reinstalling the valve train involves aligning and fitting components like lifters, rocker arms, and pushrods, ensuring proper clearance. Accessories such as magnetos, starters, and vacuum pumps are reattached with torque settings per Lycoming specs. The fuel injection system is reconnected, and linkages are adjusted for smooth operation. Final checks ensure all components are secure, properly aligned, and function as intended, restoring the engine to optimal performance and reliability.
Reassembly and Testing
Reassembly includes precise alignment of components, torque specifications, and leak testing. Post-reassembly, compression checks and final inspections ensure the engine is airworthy and ready for installation.
5.1 Torque Specifications and Alignment
Proper torque specifications are crucial during reassembly to ensure structural integrity and prevent damage. Each component, such as cylinder heads and rocker arms, must be torqued to Lycoming’s precise specifications. Alignment of parts like the crankshaft and camshaft is equally vital, requiring careful measurement and adjustment to maintain engine balance. Adhering to these steps ensures smooth operation, optimal performance, and longevity of the overhauled engine. Always refer to the official overhaul manual for exact torque values and alignment procedures to avoid costly errors.
5.2 Leak Testing and Compression Checks
Leak testing and compression checks are essential to verify engine integrity post-overhaul. Use a compression gauge to measure cylinder pressure, ensuring readings fall within Lycoming’s specifications. Pressure testing the cooling system and oil galleries helps detect any hidden leaks. These tests confirm the effectiveness of rebuilt components, such as piston rings and valves, and ensure proper engine sealing. Any deviations from acceptable limits must be addressed before engine startup to prevent damage or failure during operation.
5.3 Final Inspection and Preparation for Installation
Following successful testing, conduct a final inspection to ensure all components are properly installed and secured. Verify repairs, torque specifications, and alignment. Check for any residual leaks or issues. Prepare the engine for installation by reconnecting external systems and ensuring proper fluid levels. Apply a protective coating to exposed surfaces to prevent corrosion. Document all findings and ensure compliance with Lycoming’s specifications. Finally, review startup procedures and break-in guidelines to ready the engine for its first post-overhaul operation.
Post-Overhaul Maintenance
After overhaul, follow Lycoming’s break-in procedures, conduct regular inspections, and monitor performance. Adhere to scheduled maintenance intervals and address any post-overhaul issues promptly to ensure reliability.
6.1 Break-In Procedures for the Overhauled Engine
Proper break-in after an overhaul is crucial for the Lycoming O-360 engine. Run the engine at 1200 RPM for one minute, then increase to 1800 RPM for 20 seconds. Repeat this process to ensure piston rings seat correctly. Use straight mineral oil with the correct viscosity during the break-in period. Avoid high power settings and sudden throttle changes. Monitor oil consumption and engine performance closely during the initial operational hours. This ensures optimal engine longevity and reliability.
6.2 Scheduled Maintenance Intervals
Regular maintenance is essential for the Lycoming O-360 engine. Oil and filter changes are required every 50 hours, while spark plug inspections and compression checks should be performed every 100 hours. At 500-hour intervals, a detailed inspection of the engine, including cylinder compression and valve train components, is recommended. Adhering to these schedules ensures optimal performance, prevents premature wear, and maintains compliance with FAA regulations. Proper maintenance routines help extend the engine’s service life and reliability.
6.3 Troubleshooting Common Post-Overhaul Issues
After an overhaul, common issues with the Lycoming O-360 engine may include oil leaks, low compression, or improper fuel flow. These problems often stem from incorrect torque specifications or faulty reassembly. Operators should check for signs of vapor lock, especially in fuel-injected models, and ensure proper engine break-in procedures. Consulting the overhaul manual and adhering to Lycoming’s guidelines is crucial for diagnosing and resolving these issues efficiently. Regular post-overhaul inspections and maintenance can prevent costly repairs and ensure reliable engine performance.