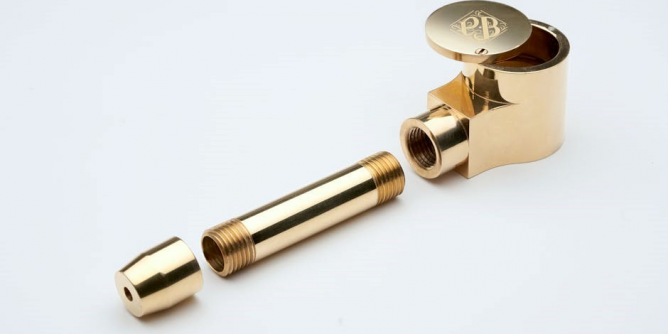
Definition and Basics of NPT Pipe Thread Chart
NPT (National Pipe Taper) refers to a standard for tapered pipe threads, ensuring leak-free connections in piping systems. The chart provides essential dimensions, tolerances, and specifications for NPT threads, including nominal sizes, threads per inch (TPI), and taper rates, critical for proper fitting installation and sealing in various applications.
1.1 What is NPT?
NPT (National Pipe Taper) is a U.S. standard for tapered pipe threads, designed to create a mechanical seal when threads are joined. It specifies dimensions, tolerances, and angles for pipe connections, ensuring compatibility and leak-free sealing. NPT threads are conical, with a 1/16-inch taper per inch, allowing them to wedge tightly together, often enhanced with sealants like PTFE tape or pipe dope for added reliability.
1.2 Importance of NPT in Pipe Fittings
NPT is vital for ensuring leak-free connections in piping systems, particularly in hydraulic and pneumatic applications. Its tapered threads create a tight seal, enhancing reliability and safety. Standardization ensures compatibility across manufacturers, simplifying installation and maintenance. NPT fittings are widely used in industries requiring precise fluid or gas control, making them indispensable for maintaining system integrity and performance.
1.3 Basic Dimensions and Tolerances
The NPT Pipe Thread Chart specifies nominal pipe sizes, threads per inch (TPI), and pitch, ensuring compatibility and proper fitting. Major and minor diameters, along with thread angles and lengths, are standardized. Tolerances are critical to ensure threads mate correctly, preventing leaks and ensuring mechanical integrity. These dimensions align with ANSI/ASME B1.20.1, providing a foundation for precise manufacturing and gaging of NPT threads.
How to Read an NPT Pipe Thread Chart
Understanding nominal pipe sizes, threads per inch (TPI), and pitch is key to interpreting the chart. Measure the thread diameter and match it to the chart for accurate identification and sizing.
2.1 Understanding Nominal Pipe Sizes
Nominal pipe sizes in NPT charts refer to the pipe’s diameter, not the actual thread size. Common sizes include 1/8, 1/4, 1/2, and 1 inch, with each size designated to fit specific thread dimensions. These nominal sizes are standardized to ensure compatibility and proper sealing when connecting pipes and fittings, making them essential for accurate thread identification and installation.
2.2 Threads per Inch (TPI) and Pitch
Threads per Inch (TPI) indicates the number of threads along a one-inch length of pipe, varying by nominal size. Common TPI for NPT threads include 27 for smaller pipes (e.g., 1/8″) and 18 for larger sizes (e.g., 1/2″). Pitch, the distance between consecutive threads, is calculated as 1 divided by TPI. This specification ensures proper thread engagement and sealing in tapered pipe connections, critical for maintaining integrity in piping systems.
2.3 Taper Rate and Angle Specifications
The NPT thread features a taper rate of 1/16 inch per inch, equivalent to a 1°47′ angle per side, totaling 60° between thread sides. This precise taper ensures threads wedge together tightly, enhancing the seal when combined with sealants like Teflon tape. The specified angle and taper are critical for achieving the desired mechanical seal in NPT connections, making it a reliable choice for various piping applications.
Common NPT Pipe Thread Sizes and Applications
NPT threads are available in standard sizes like 1/8, 1/4, 1/2, and 3/4 inches, commonly used in hydraulic, pneumatic, and industrial systems for reliable connections and sealing.
3.1 Standard Sizes (1/8, 1/4, 3/8, etc.)
Standard NPT sizes include 1/8, 1/4, 3/8, 1/2, 3/4, 1, and 2 inches. These sizes refer to nominal pipe diameters, with specific TPI and taper rates ensuring proper sealing. Commonly used in plumbing and industrial systems, these sizes are tapered, allowing threads to wedge together for a secure, leak-resistant connection, essential for hydraulic and pneumatic applications.
3.2 Usage in Hydraulic and Pneumatic Systems
NPT threads are widely used in hydraulic and pneumatic systems due to their tapered design, which ensures a tight, leak-resistant seal. The mechanical seal, often enhanced with thread sealants like PTFE tape, prevents fluid or gas leakage. This makes NPT threads ideal for high-pressure applications, ensuring reliability and efficiency in hydraulic pumps, cylinders, and other equipment where maintaining pressure integrity is critical.
3.3 Industry-Specific Applications
NPT threads are integral across industries like oil and gas, chemical processing, and construction. They are used in drilling equipment, valves, and pumps due to their leak-resistant tapered design. In hydraulic systems, NPT ensures tight connections, while in aerospace, they meet precise standards for durability. Each industry leverages NPT’s reliability and versatility to maintain performance and safety in demanding environments.
How to Measure and Identify NPT Threads
Measure thread diameter using calipers, focusing on the second or third thread. Compare measurements to NPT charts to determine nominal pipe size and thread type accurately.
4.1 Using Calipers for Accurate Measurements
Use calipers to measure the major diameter of the NPT thread, typically across the second or third thread from the end. Ensure accuracy by positioning the calipers perpendicular to the thread axis. Record the measurement and compare it to the NPT chart to determine the nominal pipe size. This method ensures precise identification of thread size and type, critical for compatibility and proper sealing in piping systems.
4.2 Determining Nominal Size from Thread Diameter
Measure the thread’s major diameter using calipers, then refer to the NPT chart to find the corresponding nominal size. The chart lists standard sizes and their respective diameters, allowing precise identification. This step ensures correct fitting selection by matching the measured diameter to the nominal size, crucial for maintaining system integrity and preventing leaks or connection issues.
4.3 Distinguishing NPT from Other Thread Types
NPT threads are identified by their tapered shape and 60-degree thread angle. Unlike straight threads like NPS, NPT’s taper creates a wedging action for sealing. Key differences include the 1/16″ taper per inch and the use of PTFE tape or pipe dope for sealing. Comparing these features with ISO or BSPT standards helps in distinguishing NPT, ensuring compatibility and proper application in piping systems.
NPT vs. Other Pipe Thread Standards
NPT is a U.S. standard with tapered threads for sealing. Unlike NPS, which is straight, NPT’s taper enhances the seal. ISO and BSPT standards differ in thread angles and pitch, affecting compatibility. Regional preferences often dictate the choice, with NPT predominant in North America and ISO/BSPT elsewhere, requiring careful consideration for international projects to ensure proper connections and avoid leaks.
5.1 Comparison with NPS (National Pipe Straight)
NPS (National Pipe Straight) differs from NPT as it features straight threads, typically used for mechanical joints requiring a sealant. While NPT’s tapered threads create a wedging action for sealing, NPS relies on additional components like gaskets or O-rings. NPS is often preferred in applications where disassembly is frequent, whereas NPT is ideal for permanent or high-pressure connections, each catering to distinct operational needs and industries.
5.2 Differences from ISO and BSPT Standards
NPT differs significantly from ISO and BSPT standards, primarily in thread geometry and application; ISO standards often use straight or tapered threads with varying pitch and diameter specifications, while BSPT (British Standard Pipe Taper) features a Whitworth thread form with a 55-degree angle. Unlike NPT’s 60-degree angle, BSPT threads are more rounded, affecting compatibility and sealing methods. These differences highlight regional preferences and the importance of matching thread standards to ensure proper connections and avoid assembly issues.
5.3 Regional Preferences and Compatibility
NPT threads are predominantly used in North America, while ISO and BSPT standards are more common in Europe and Asia. This regional preference can lead to compatibility issues when integrating components from different regions. Ensuring thread compatibility is crucial to avoid assembly problems and leaks, emphasizing the need to adhere to local standards when designing or sourcing piping systems internationally.
Gaging and Quality Control for NPT Threads
Gaging ensures NPT threads meet precise specifications, using tools like plug and ring gages to verify thread accuracy. Proper gaging is vital for maintaining thread integrity and sealability, preventing leaks and ensuring reliable connections in piping systems. Regular quality control checks are essential to uphold manufacturing standards and performance.
6.1 Importance of Proper Gaging
Proper gaging ensures NPT threads meet specified tolerances, crucial for achieving leak-free connections and mechanical strength. Accurate gaging verifies thread dimensions, preventing assembly issues and ensuring compatibility. It guarantees compliance with standards, maintaining product quality and reliability, while avoiding costly rework or replacement due to faulty threads.
6.2 Types of Gages (Plug and Ring Gages)
Plug gages measure internal threads, ensuring correct diameter and taper, while ring gages check external threads. Both types verify thread angles and pitch. They ensure threads meet NPT standards, preventing assembly errors. Proper use of these gages is vital for maintaining quality and functionality in pipe connections, ensuring reliability and safety in various applications.
6.3 Ensuring Thread Accuracy and Sealability
Ensuring thread accuracy involves precise gaging to verify dimensions and tolerances. Sealability is achieved through proper thread engagement and the use of sealants like Teflon tape or pipe dope. Regular inspections and adherence to NPT standards prevent leaks and ensure reliable connections, maintaining system integrity and performance over time.
Best Practices for Using NPT Pipe Thread Charts
Always use the chart to select correct thread sizes and materials. Apply thread sealants like Teflon tape for leak-free connections. Ensure proper tightening without over-tightening. Follow manufacturer guidelines for optimal safety and efficiency.
7.1 Selecting the Right Thread Sealants
Choosing the correct sealant for NPT threads is crucial for ensuring leak-free connections. Common options include Teflon tape and pipe dope, designed to fill microscopic gaps between threads. Always select a sealant compatible with the system’s operating conditions, such as temperature and chemical exposure. Apply sealants sparingly but evenly to avoid over-tightening, which can damage threads. For optimal results, consult the NPT chart for recommendations on sealant types and application methods.
- Ensure compatibility with fluid and environmental conditions.
- Apply 2-4 wraps of Teflon tape for most applications.
- Avoid over-tightening to prevent thread damage.
7.2 Avoiding Common Mistakes in Thread Installation
Avoid over-tightening, which can damage threads and compromise the seal. Ensure threads are clean and free of debris before assembly. Use the correct thread sealant and apply it evenly. Never force threads together, as this can lead to cross-threading. Always refer to the NPT chart for proper torque specifications and thread engagement lengths. Improper installation can result in leaks or thread damage, requiring costly repairs.
- Prevent over-tightening to avoid thread damage.
- Ensure proper alignment to prevent cross-threading.
- Follow NPT chart guidelines for secure connections;
7.3 Maintenance and Inspection Tips
Regularly inspect NPT threads for wear, rust, or damage. Clean threads thoroughly before reassembly to ensure proper sealing. Replace worn or damaged threads promptly to prevent leaks. Apply thread sealants as needed to maintain integrity. Schedule periodic checks of all connections, especially in high-pressure or corrosive environments, to ensure long-term reliability and safety in piping systems.
- Inspect threads for wear or corrosion regularly.
- Clean and maintain threads to prevent contamination.
- Replace damaged threads to avoid leaks and failures.