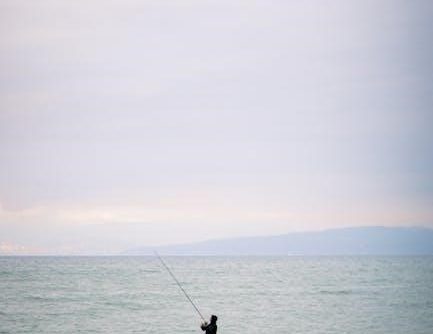
Tungsten guide rods are precision-engineered components made from tungsten, a dense, hard metal. They are widely used in industrial and mechanical systems for their exceptional durability and resistance to wear. Known for their high density and thermal stability, these rods play a critical role in guiding and stabilizing moving parts in machinery. Their unique properties make them indispensable in various industries, ensuring smooth operation and longevity in demanding environments.
1.1 What Are Tungsten Guide Rods?
Tungsten guide rods are high-performance components made from tungsten, a rare, dense metal known for its exceptional hardness and wear resistance. These rods are designed to provide precise guidance and stability in mechanical systems, often used in demanding industrial environments. Their durability and ability to withstand extreme conditions make them ideal for applications requiring minimal wear and long service life.
1.2 Importance of Tungsten in Industrial Applications
Tungsten’s exceptional hardness, density, and thermal resistance make it a cornerstone in industrial applications. Its ability to withstand extreme temperatures and wear ensures reliability in high-stress environments. Tungsten guide rods, in particular, are vital for maintaining precision and stability in machinery, reducing downtime and extending equipment lifespan. Their durability and performance justify their widespread use in demanding industrial settings.
Properties of Tungsten
Tungsten exhibits high density, hardness, and thermal resistance, making it ideal for demanding applications. Its corrosion resistance and ability to withstand extreme temperatures enhance its industrial versatility and reliability.
2.1 High Density and Hardness
Tungsten’s exceptional density and hardness make it a premium material for guide rods. With a density of ~19.3 g/cm³ and a Mohs hardness of 8.5-9, tungsten ensures minimal deformation under stress. Its high Young’s modulus (~400 GPa) provides rigidity, crucial for precise guidance in industrial machinery. These properties enhance durability and stability, making tungsten guide rods ideal for high-performance applications where reliability and longevity are paramount.
2.2 Thermal and Corrosion Resistance
Tungsten guide rods exhibit remarkable thermal and corrosion resistance, vital for high-temperature environments. With a melting point of 3422°C, tungsten maintains structural integrity under extreme heat. Its natural oxide layer provides corrosion resistance, reducing wear from harsh chemicals. This combination ensures consistent performance and durability in industrial settings, minimizing downtime and extending service life, making tungsten guide rods a reliable choice for demanding applications.
Manufacturing Process of Tungsten Guide Rods
Tungsten guide rods are crafted through precise machining and advanced manufacturing techniques. High-quality tungsten material is carefully selected, shaped, and treated to ensure optimal performance and durability.
3.1 Material Selection and Machining
Material selection is critical for tungsten guide rods, focusing on high-purity tungsten alloys for optimal density and hardness. Machining involves advanced CNC techniques and diamond-coated tools to achieve precise dimensions. The process requires careful handling due to tungsten’s hardness and brittleness, ensuring minimal material waste and high surface finish quality. This step is pivotal for the rod’s final performance and durability.
3.2 Heat Treatment and Surface Finishing
Heat treatment enhances tungsten guide rods’ mechanical properties, involving high-temperature processes to achieve desired hardness and toughness. Surface finishing techniques, such as grinding, polishing, or applying protective coatings, ensure smooth operation and corrosion resistance. These steps are essential for optimizing performance, extending lifespan, and meeting specific industrial requirements. Precision finishing ensures dimensional accuracy and surface quality, critical for guide rods’ functionality in demanding applications.
Applications of Tungsten Guide Rods
Tungsten guide rods are widely used in industrial machinery for their durability and resistance to wear. They are also utilized in firearms for recoil management and stability.
4.1 Use in Industrial Machinery
Tungsten guide rods are extensively used in industrial machinery due to their high density and hardness, making them ideal for heavy-duty applications. They are employed in manufacturing, construction, and automotive industries to guide moving components with precision. Their resistance to wear and deformation ensures prolonged machinery lifespan, reducing downtime and maintenance costs. This makes them a critical component in enhancing operational efficiency and overall machine performance.
4.2 Role in Firearms and Recoil Systems
Tungsten guide rods are valued in firearms for their high mass and rigidity, which helps mitigate recoil and improve accuracy. Their dense material absorbs and distributes recoil energy effectively, reducing muzzle rise. This enhances stability and control, especially in rapid-fire scenarios. The rods’ durability ensures consistent performance under harsh conditions, making them a reliable choice for recoil systems in both civilian and tactical firearms applications.
Comparison with Other Materials
Tungsten guide rods excel due to their exceptional density, hardness, and thermal resistance. Compared to steel or ceramic, tungsten offers superior durability and stability in extreme conditions.
5.1 Tungsten vs. Steel Guide Rods
Tungsten guide rods surpass steel in density, hardness, and wear resistance, making them ideal for high-stress applications. Steel, while more affordable and versatile, lacks tungsten’s thermal stability and durability. Tungsten’s ability to maintain precision under extreme conditions makes it the preferred choice for industrial and specialized machinery, despite its higher cost and complexity in manufacturing compared to steel alternatives.
5.2 Tungsten vs. Ceramic Guide Rods
Tungsten guide rods offer superior density and hardness compared to ceramic ones, making them more durable in high-stress environments. Ceramics, however, excel in corrosion resistance and are lighter, ideal for high-temperature applications. While tungsten is better for heavy-duty machinery, ceramics are preferred in corrosive or weight-sensitive scenarios, balancing performance based on specific industrial needs and operational conditions.
Maintenance and Care
Regular cleaning with non-abrasive materials and proper storage in dry conditions are essential. Handling with care avoids damage, ensuring longevity and performance of tungsten guide rods.
6.1 Cleaning and Storage
Cleaning tungsten guide rods requires mild detergents and soft cloths to prevent scratches. Avoid harsh chemicals or abrasive materials. Store them in a dry, cool place, away from direct sunlight. Proper maintenance ensures their durability and prevents corrosion, which is crucial for optimal performance in industrial applications. Regular inspections can help identify potential issues early, extending their service life.
6.2 Inspection and Replacement
Regular inspection of tungsten guide rods is essential to identify wear, damage, or corrosion. Check for surface cracks, excessive scratches, or deformation. Replace rods if damage is detected to prevent system failure. Inspections should be conducted by qualified personnel, following manufacturer guidelines. Replace rods as recommended or when performance degrades. Always use authentic tungsten rods for optimal safety and performance. Document inspections and replacements for future reference.
Safety Considerations
Handling tungsten guide rods requires care due to their hardness and brittleness. Wear protective gear to prevent injury from sharp edges or fragments. Follow installation and operational guidelines to ensure safe use and avoid mechanical failure. Regular inspections are crucial to maintain safety standards and prevent accidents. Always prioritize proper handling techniques to minimize risks.
7.1 Handling Precautions
When handling tungsten guide rods, wear protective gloves and eyewear to prevent injury from sharp edges. Ensure a firm grip to avoid dropping, as tungsten’s brittleness can lead to cracking. Store them in a dry, secure location to prevent damage or corrosion. Use appropriate tools for installation and avoid applying excessive force, which may cause breakage. Regularly inspect for wear or damage before use.
7.2 Operational Safety Guidelines
Ensure proper alignment and secure installation of tungsten guide rods to prevent misoperation. Avoid exceeding load limits to minimize risk of breakage. Use appropriate tools and follow torque specifications. Monitor for signs of excessive wear or heat buildup during operation. Regularly check for debris or contamination that may affect performance. Immediate shutdown is recommended if unusual vibrations or noises occur to prevent potential failure and ensure system safety.
Cost Considerations
Tungsten guide rods are a significant investment due to tungsten’s rarity and high production costs. However, their exceptional durability and longevity often justify the initial expense in industrial settings.
8.1 Initial Investment vs. Longevity
Tungsten guide rods require a higher initial investment due to the cost of raw materials and manufacturing. However, their exceptional hardness, durability, and resistance to wear ensure a longer service life compared to alternatives. This longevity reduces maintenance and replacement costs over time, making them a cost-effective choice for industrial applications despite the upfront expense.
8.2 Value for Money in Industrial Settings
Tungsten guide rods provide exceptional value in industrial applications due to their durability and low maintenance. Their high density and resistance to wear ensure consistent performance, reducing downtime. Despite a higher initial cost, long-term savings from extended service life and fewer replacements make them a cost-effective choice for demanding industrial environments, enhancing operational efficiency and productivity significantly.
Future Developments
Research and development in tungsten alloys are expected to enhance guide rod performance. New applications in renewable energy and aerospace may emerge, driving innovation further.
9.1 Innovations in Tungsten Alloys
Recent advancements in tungsten alloy manufacturing focus on improving strength-to-weight ratios and corrosion resistance. Researchers are developing nanostructured tungsten alloys for enhanced performance in extreme environments. Additionally, hybrid alloys combining tungsten with other refractory metals are being tested for superior thermal conductivity and durability. These innovations promise to expand the versatility of tungsten guide rods in high-temperature and high-stress applications, ensuring their continued relevance in evolving industries.
9.2 Emerging Applications
Tungsten guide rods are expanding into new sectors, including renewable energy systems and advanced medical devices. Their high density and hardness make them ideal for precise movements in robotic arms and next-generation industrial automation. Additionally, their thermal resistance is being leveraged in high-temperature aerospace applications, such as satellite components. These emerging uses highlight tungsten’s versatility in meeting modern technological demands for durability and precision.
Tungsten guide rods are indispensable in modern machinery due to their exceptional strength, durability, and resistance to wear. Their versatility ensures continued relevance across various industrial applications, making them a cornerstone of precision engineering and a vital component for future advancements.
10.1 Summary of Key Points
Tungsten guide rods are highly durable components with exceptional hardness, density, and resistance to thermal and corrosive environments. Their precision engineering ensures longevity and reliability in industrial machinery. Widely used in firearms and heavy-duty applications, they offer superior performance compared to steel or ceramic alternatives. Proper maintenance and safety precautions are essential to maximize their lifespan, making them a cost-effective choice for demanding industrial settings.
10.2 Final Thoughts on Tungsten Guide Rods
Tungsten guide rods are a testament to modern engineering, offering unparalleled durability and performance. Their exceptional hardness, density, and resistance to extreme conditions make them indispensable in industrial and precision applications. While the initial cost may be higher, their longevity and reliability provide long-term value. As industries evolve, tungsten guide rods remain a critical component, ensuring efficiency and stability in demanding environments.